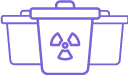
Packaging Intermediate-level waste
Compaction for hulls and end caps…
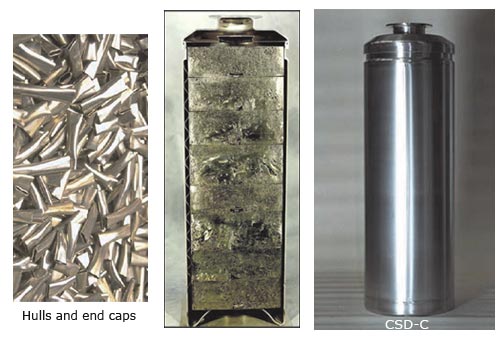
Cross-section of a container of compacted ILW-LL waste
The stainless steel container on the right is 1,335 m high with a diameter of 43 cm. The waste package has a volume of 183 litres and weighs approximately 700 kg, of which waste represents 600 kg and the container 92 kg.
© AREVA
The zirconium alloy cladding around the uranium oxide pellets is strongly irradiated while inside the reactor. Although zirconium is neutron-transparent, the cladding becomes radioactive. The radioactivity level is high enough for cladding materials to be treated as intermediate-level long-lived waste (ILW-LL).
During reprocessing, the cladding hulls are separated from the grids and end caps that hold them together, then sheared into 3.5 cm long fragments that fall into a bath of nitric acid. When the fuel pellets have dissolved, the metal fragments are rinsed, collected and stored underwater pending conditioning.
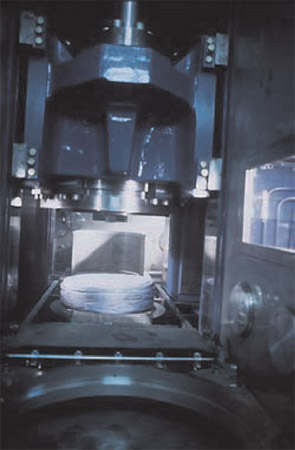
Compaction
Cladding hulls and end caps that will become category B intermediate-level, long-lived waste are placed in cartridges and then compacted. The resulting disks are stacked in a stainless steel container (CSD-C canister).
© AREVA/DR
The cladding hulls and end caps are then placed into cartridges and compacted into discs. The discs are stacked inside a container of the same shape and dimensions as the container used for vitrified waste.
Standard compacted waste containers (CSD-C) contain 90% hulls and end caps and approximately 10% of miscellaneous solid operating waste. The main contributor to this waste’s radioactivity is nickel-63, a long-lived beta and gamma emitter; as a result, this waste is classified as intermediate-level long-lived waste.
Using the same standard for different types of waste container simplifies handling and interim storage operations. Looking ahead, it will also facilitate disposal. The hull compacting shop (ACC), which has been operating since 2002, provides significant benefits compared with earlier bitumenised and concrete-based conditioning processes.
The introduction of compaction has greatly reduced the volume of ILW-LL waste generated by reprocessing spent fuel. Roughly one 183 litre, 700 kg container of compacted hulls and end caps is required per tonne of spent fuel (heavy metal), representing a total of 850 packages per year, for the 850 tonnes of French fuel processed annually.
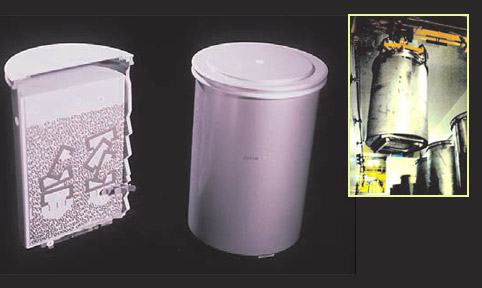
Before compacting, cement and bitume …
Compacting resulted in better conditioning and smaller volumes of ILW-LL. Previously, such waste were embedded in an inert cement or bitume material. Between 1990 and 1995, cladding hulls and end caps were placed together in a stainless steel drum that was then filled with a cement slurry. The filled drums were then decontaminated, then covered, prior to disposal in a storage workshop (image on right).
© AREVA
Compacted waste packages are cold packages that release only around 20 watts – one-fifth of the output of a 100 W incandescent light-bulb – at the time of production. They do not present any radiological risks. They are stored in a purpose-built compacted waste store at the facility in La Hague, pending a decision regarding their ultimate fate.
Other ILW-LL waste: cementitious and bituminous waste and technological products
Low- and intermediate-level effluents and sludge from reprocessing operations are another source of ILW-LL waste. Effluents have been decontaminated by chemical co-precipitation at the STE3 facility in La Hague since 1989. The precipitates (dehydrated sludge), in which the effluents’ activity is immobilised, are subsequently bitumenised and conditioned in stainless steel drums. The new effluent management strategy implemented in La Hague has reduced the quantity of effluents processed in STE3, and hence the corresponding number of bitumen drums produced.
Certain technological waste rich in alpha emitters is characterised by high contents of potentially gas-producing organic matter. An ongoing project by ANDRA, Areva and the CEA aims to develop a plasma torch incineration process to mineralise such organic matter and incorporate the resulting ash into a glass material. This would considerably reduce waste volumes and eliminate gas-related risks. According to ANDRA, such a process would enable 4,700 m3 of such waste to be treated by 2040.
Other articles on the subject « Waste Conditioning »
Vitrified High Level Waste
Glass – A very resistant matrix for high-level waste After the uranium and plutonium have b[...]
Resistance of R7T7 glass
Assessing the resistance of vitrified waste over millennia Is nuclear power a clean industry? To [...]
Conditioning Spent Fuel
Underground disposal of spent fuel – A long-term option Spent fuel assemblies unloaded from react[...]
Low and very low level waste
Basic conditioning for low-level and very low-level waste Waste in which the radioactivity is low[...]
Radioactive Waste Containers
Canisters and containers for various types of waste France’s National Evaluation Commission[...]